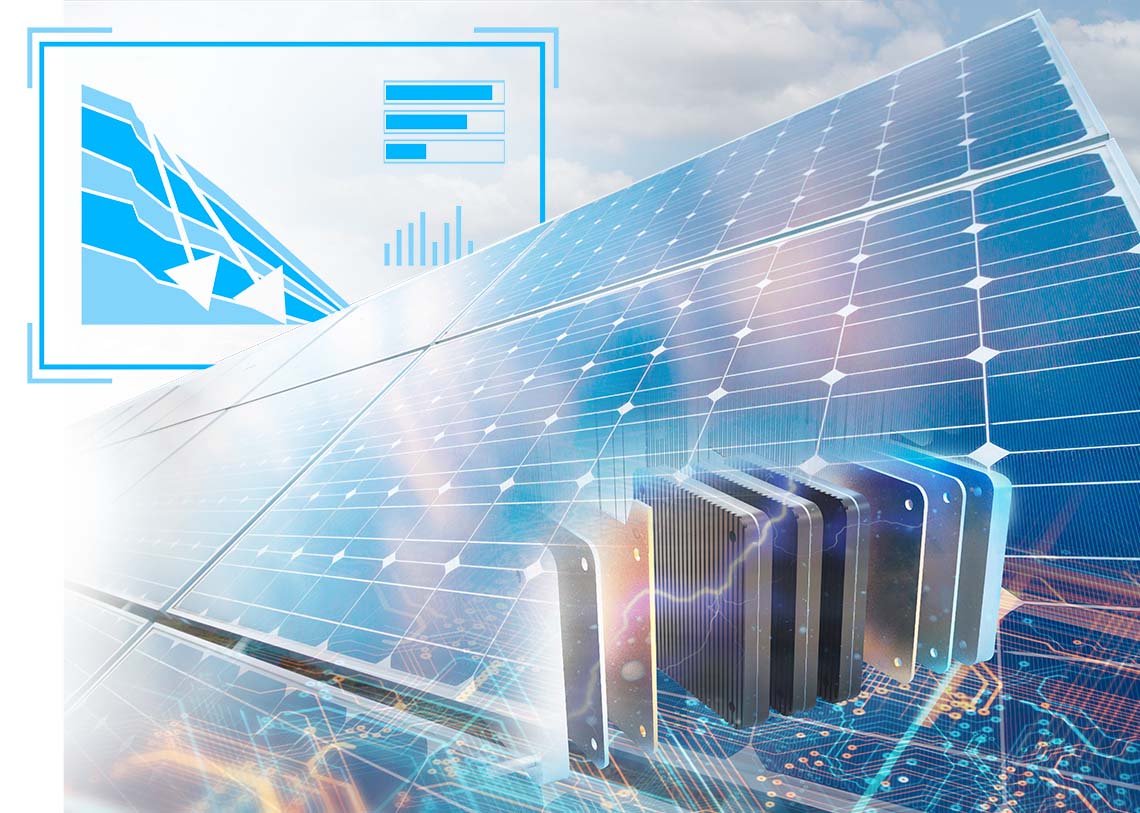
NEW ENERGIES
For more than 70 years we support our customers in the development and implementation of individual technical solutions in the field of Coating and Converting, also in the paper finishing – from the conception via detailed tests in our laboratories, the manufacturing and assembly up to the modifications of existing lines.
More than 70 different coating processes which we can also apply in our laboratories form the basis for designing optimal processes that focus on maximum reliability, precision and the avoidance of rejects and are designed optimally for the industrial 24/7 continuous use.
An efficient, energy saving and pinpoint drying / crosslinking is an essential part of the coating lines. Thermal drying processes with lowest tolerances, also supported by IR technology and remoistening, form the basis for products at the highest level of quality.
The energy sector, including the area of clean room and GMP applications, is a very important component for us. Using our own technical center, we are also able to combine known technologies to develop new machine concepts or procedures, so that innovative new products are created that enable a competitive advantage.
> Take a look in our joint brochure with Saueressig Group <
You are looking for individual technical solutions at the highest level of quality?
- A wide range of industries served with state-of-the-art coating lines:
- Battery industry
- Electrode coating
- Separator films
- Battery wrapping
- Fuel Cells and Electrolysis
- Membranes
- CCM
- GDL
- Photovoltaics
- Silicon based
- Pervoskite based
- Printed Electronics
- Battery industry
- A wide range of coating applications
- Slot Die Coating
- Intermittent coating
- Simultaneous double sided coating
- Pattern coating
- Stripe coating
- Comma Bar Coating
- Knife over Roll Coating
- Pressure Gravure Coating
- Slot Die Coating
- Dedicated drying technology
- Air drying with high temperature range
- Floatation drying
- Roller supported drying
- IR-Drying
- Air drying with high temperature range
Battery separator film
Discover our line concepts for the efficient production of battery separator film – consistent high quality coating speeds of 400 m/min enable significant production savings.
COATING
Versatility and precision are the keys to high quality in coating processes. OLBRICH offers the right technology for every requirement: From less than 1g / m² to several 1,000 g / m² of application weight, from production speeds of less than 1 m / min to more than 1,000 m / min, and all of that at very different properties of the coating media.
Exemplary coating technologies:
- Slot die coating (intermitted and double sided simultaneous)
- Comma bar
- Roll coating (intermitted and double sided simultaneous)
DRYING
The productivity of machines and lines for both solvent-based and water-based as well as various so-called 100% coating media is essentially determined by the selected dryer and other heat treatment measures. We implement high energy efficiency for the drying process as well as optimal adaptation to the needs of the products and select the appropriate drying process from our extensive range.
With our solutions for drying, you can rely on the highest quality, maximum safety and optimum energy efficiency. As we design every system and machine precisely for your products, you always achieve uniform and gentle drying results over the entire width and length. This also applies to thin and tension-sensitive films.
Our specialists implement a wide variety of dryer and nozzle concepts for you in all performance and size classes - from nozzle-type air recirculation dryers to clean room dryers and floatation dryers with special floatation nozzle technology.
At the same time, you can always rely on the performance of your systems: you achieve a high level of efficiency by using the latest high-performance components while at the same time ensuring gentle web transport - even with low web tensions.
You are free to determine the energy source of your drying systems. From oil, gas and steam to electrical heating.
Exemplary drying technologies:
- Speed-Star® air recirculation system
- Easy Clean® for easy cleaning
- Vacutex® nozzle system
- Nozzle-type air recirculating dryer with internal/external air recirculation
- Cleanroom/GMP dryer and/or according to FDA standard
- Roller dryers
- Upper and lower air dryer, also with separate temperature control
- CTS bottom- and TP top air nozzles
- Floatation dryer with floatation nozzle technology
- IR field dryer, plate dryer
- Circulating air cooling zones with external air recirculation ducting
- liftable systems
WINDING
Thanks to our special expertise in the field of winding films and foils, there are no limits for your company: our specialists will implement machines and systems for you for all conceivable winding variants - in any desired working width, for all speeds and materials. For quality assurance reasons, we rely exclusively on our own state-of-the-art technology, both for single winders and for automated turret winders.
Especially for the lab scale demands we use our own cantilever design and technology to achieve the best accessibility and cleanability in your line.
Exemplary winding technologies:
- Single-station winders
- Turret winders for continuous plant operation
- Splicing equipment
- Pneumatic or motorized impact knife
- Automatic loading and unloading
TREATING
Vacuum rollers separate tensions between two production steps without touching the outer coated surface.
For films, a mesh screen grants that no marks are left on the substrate, at selected places such as the dryer outlet. Mesh screens can be quickly and easily changed. Vacuum rollers are available with a width adjustment feature, either manual or automatic.
Services in a full-service package
We implement your individual project in six carefully coordinated steps:
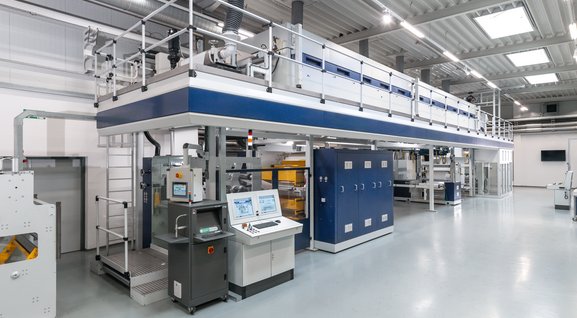